1. Information
- Industry: Plastic Injection Molding
- Scale: Over 1,000 workers
- Number of machines: 200
- Number of molds: 150
2. Challenges
2.1 Delivery and Storage
As a major player in the plastic injection molding industry, the company faces numerous challenges in managing delivery and storage. Key issues include:
– High Volume and Stringent Delivery Demands:
- The company consistently handles a large volume of orders. This requires maintaining a safe inventory level to meet delivery demands. Even when there are sudden spikes in delivery needs, the company must ensure there is enough stock to prevent disruptions in delivery schedules and quantities to customers
– Frequent Changes in Delivery Schedules:
- The delivery plans are frequently altered, necessitating continuous adjustments in production schedules. This instability makes forecasting and managing production extremely challenging
– Limitations of Excel in Production Management:
- Currently, the company uses Excel for production planning. However, Excel lacks the flexibility to handle sudden and complex changes in production and delivery schedules. This results in stock shortages when needed and excessive storage of unnecessary items, wasting resources and storage space.
2.2 Machinery and Mold Management
Besides delivery and storage issues, the company also faces numerous challenges in managing machinery and molds:
– Detailed Production Planning:
Creating detailed production plans for each mold and based on material characteristics is highly complex. The company must ensure that each mold is used most efficiently to meet production requirements.
– Maintenance Alerts for Molds:
- Machinery and molds require regular maintenance. However, the lack of timely alert systems can lead to unexpected breakdowns, causing production disruptions and expensive repair costs.
3. IVS Solution
Based on the challenges and requirements of the client, IVS surveyed, developed, and implemented a management software for delivery and production planning with the following key features:
3.1 Optimized Production Planning:
- The system automatically calculates capacity and recreates the production plan when there are changes in quantity and delivery dates.
- The system manages mold productivity, assigning which molds can run on which machines to optimize production output
3.2 BOM
– Material Composition Management:
The solution manages the Bill of Materials (BOM) for finished products with the same materials or characteristics, consolidating them during production planning to minimize mold changeover time. This reduces time and costs associated with changing molds and materials.
3.3 Maintenance Alerts
-Shot Count Alerts:
The system provides timely alerts on the number of shots (a shot in the plastic injection molding industry refers to one complete cycle of injecting plastic into a mold to create a specific product or part) used, calculating the remaining shots to alert for mold maintenance. This prevents unexpected breakdowns and ensures machinery operates at its best.
3.4 Production Management Reports
Real-Time Production Management:
The system provides real-time production management reports, allowing managers to easily grasp the current situation and make accurate decisions. This not only improves production efficiency but also enhances the company’s competitiveness.
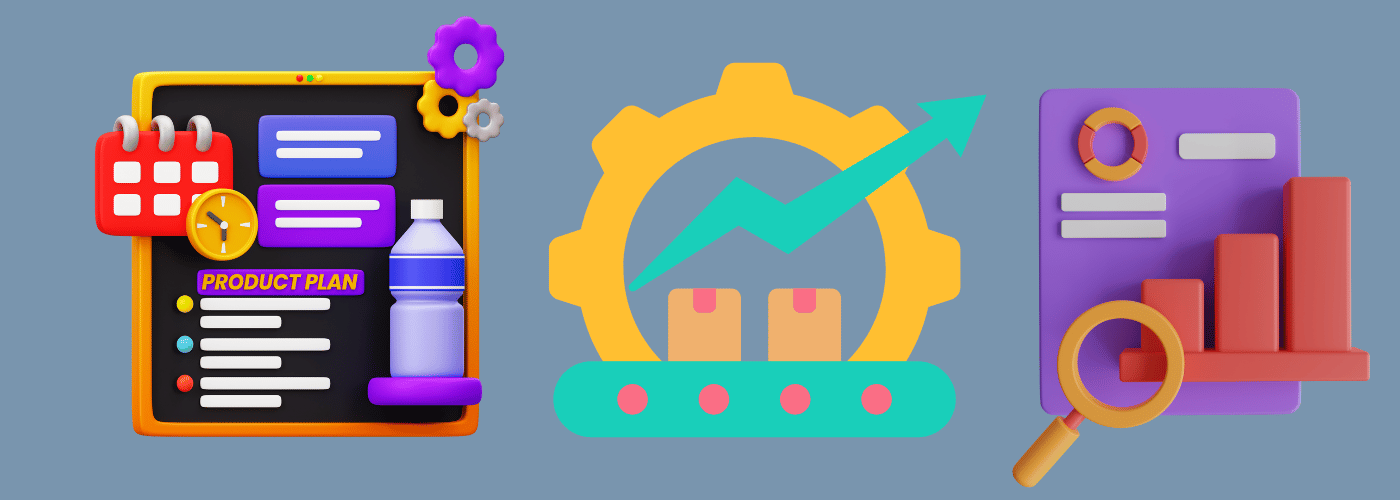
4.Achieved Results
– Minimized Errors When Using Excel:
- The system automatically calculates and plans production accurately, minimizing errors that occur when using Excel. This helps clients optimize their production processes, reducing material and labor waste.
– Quick Information Retrieval:
- Information is quickly accessible through the system.
– Improved Inter-Departmental Coordination:
- Coordination between departments according to the company’s processes is improved..
-Reduced Labor Costs
- The system’s automated calculations and optimized production and delivery planning lead to savings in labor costs for manual production planning.
– Storage Cost Savings:
- The system prevents over-purchasing materials, reducing storage costs.
- Production is meticulously planned, avoiding the production of unnecessary stock, and minimizing unnecessary inventory.
– Reduced Stock Shortages:
- Ensures a safe inventory level and minimizes stock shortages.
5. Conclusion
Implementing IVS’s production and delivery management software has provided significant benefits to the plastic injection molding company. The solution has optimized production processes, minimized errors, and reduced costs, thereby enhancing operational efficiency and better meeting customer demands.